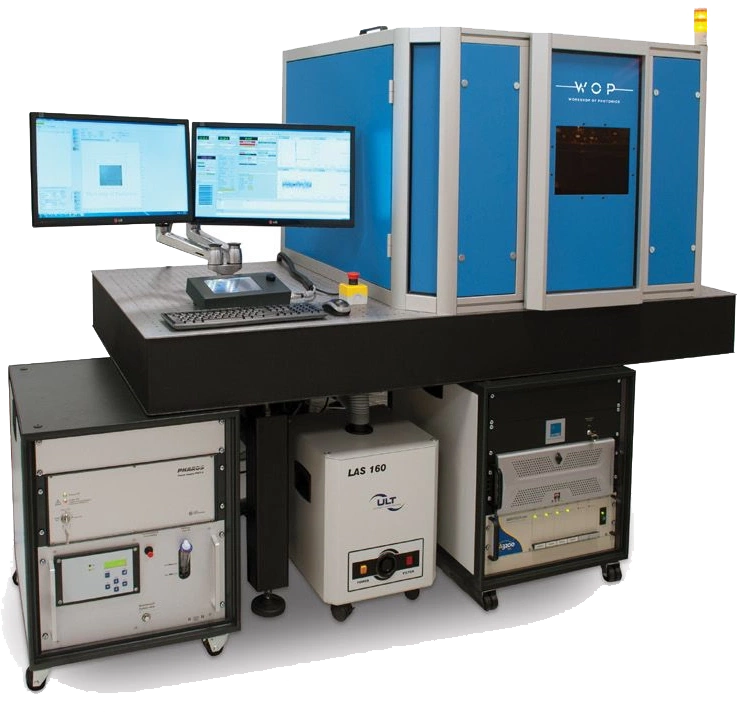
FemtoLAB
A Femtosecond Laser Micromachining Workstation
The perfect choice for scientific laboratories and R& D centers that require custom solutions for various tasks. The System offers submicron resolution, high speed. Ultra-high precision results and top-quality components.
Main Features of the FemtoLAB
- Complex objects can be fabricated with sub-micron resolution
- Ultra-high precision micromachining
- High Speed
- Efficient beam delivery and power control
- High-end industrial-grade femtosecond laser
- High-performance galvanometer scanners
- Highest Quality Optical Components
- High Accuracy Positioning Stages
- Object movement and laser pulse synchronization in time and space
- Unique software interfaces with controls on all hardware units
Technical Specifications
Technical specifications depend on individual requirements needed to implement set tasks therefore the information may vary in the range listed.
Parameter | Value |
---|---|
Pulse Duration | 40 fs – 10 ps |
Repetition rate | 1 kHz – 2 MHz (Single-Shot, Pulse-on-Demand, Burst Mode) |
Average power | Up to 80W |
Pulse energy | Up to 2 mJ |
Wavelength | 1030 nm, 515 nm, 343 nm, 257 nm |
Positioning accuracy | ± 250 nm |
Travel range | From 25×25 mm to 500×500 mm (larger on request) |
Reasons to choose a FemtoLAB
Flexibility
The FemtoLAB has the capabilities to provide multiple custom solutions for various tasks. It is an entire laser laboratory on an optical table. It is equipped with a high-end industrial-grade femtosecond laser, high accuracy linear positioning stages, high performance galvanometer scanners and versatile micromachining software SCA. This established workstation saves experimenting time and easily facilitates the training of new users. It is a flexible system that allows easy expansion and upgrading.
- Laser Source
- Sample Positioning System
- Beam Delivery
- Laser Power and Polarization Control
- Software for System Control (Autofocus and Machine Vision upon request)
- Sample Holders and special mechanics (sampling handling automation on request)
- Optical Table
- Enclosure (full or partial)
- Dust removal unit
- The Laser System is automated with SCA micromachining software that is an essential part of the Laser System and is not sold separately
Benefits of the FemtoLAB
Custom Built
Every workstation is built to provide you with the results you need
Upgradable
Additional functions can be added to your system as you need them
Flexible
A FemtoLAB workstation can be built to produce several applications
Full Support
We install your workstation at your facility and train your staff
Adaptable
A FemtoLAB can be utilized in a diverse range of businesses, research Universities or multiple other organizations
One Year Warranty
After warranty service is also available
Proven and Tested
FemtoLAB Workstations are chosen by research institutes and top universities and R&D centers worldwide.
Applications
Laser Micro Drilling
Laser Micro Drilling ensures high drilling speeds, good surface quality and a wide range of hole diameters. The holes are drilled with a controlled taper in various materials even those that are hard and fragile.
Glass Drilling
Laser drilling of glass utilizes femtosecond lasers is a state-of-the-art technique that has multiple advantages over conventional laser processing, mechanical drilling, or lithography.
Depending upon the application, we use conventional laser drilling techniques as well as unique Workshop of Photonics developed methods to achieve the highest quality in the market.
Advantages: Lower costs, minimal surface finish needed and ultra-high accuracy.
- No melting & micro-cracks in peripheries
- Aspect ratio up to 1:100
- Possibility for very densely packed hole arrays
- Zero tape
Note: Alternate processing parameters can be developed upon request.
Sapphire Drilling
Laser drilling of sapphire uses femtosecond laser radiation, a unique processing technique that enables no cracks in hole peripheries, accurate taper control and smooth wall finish. Workshop of Photonics continues the development of sapphire drilling techniques to meet the customers’ needs.
Advantages: Ultra-high accuracy, reliable process control, minimal or no post-processing is needed
- No melting or micro cracks in peripheries
- Accurate taper control
- Smooth inner surfaces finish
- Minimized stress area around drilled holes
Note: Alternate processing parameters can be developed upon request.
Metal Drilling
Laser drilling of metal alloys brings high quality and precision for many applications – filters, functional surfaces, fuel delivery systems and many more.
Advantages – high processing speeds with high accuracy and good surface finish
- No melting and thermal impact in peripheries
- Holes diameter from micrometer range micrometer to centimeter range
- Precise control of taper angle
- Variable geometry of holes
- Different processing parameters might be developed upon request.
Ceramics Drilling
Ceramics has unique properties and has become a leading material in the communications industry. The WOP unique femtosecond laser capabilities coupled with precise processing methods offer customers leading market services.
The system offers hole diameters from a few micrometers to tens of millimeters at a very competitive price.
- No cracking of the material
- Accurate taper Control – positive, negative or zero taper
- High aspect ratio
- Possibility of drilling blind & through holes
Optical Fibers Drilling
Laser drilling of optical fibers using femtosecond laser radiation is a state-of-the art technique showing many advantages over conventional laser processing, mechanical drilling that enable precise process control.
Advantages: High processing speed, lower costs and higher accuracy
- No melting & micro-cracks in peripherals
- Hole diameters as small as 10 µm
- Precise control of taper angle & depth
- Variable geometry of holes
Note: Alternate processing parameters can be developed upon request.
Laser Micro Cutting and Dicing
Glass Cutting
The Laser cutting (scribing) process is optimized for each type of glass (Tempered and non-tempered). The processing window is wide and can be easily set up to various parameters.
- Straight & round cut trajectories
- Thickness of tempered glass from 0.3 mm to 1.3 mm
- Thickness of non-tempered glass from 0.03 mm to 1 mm
- DOL of tempered glass from 10µm to 80 µm
- Cutting speed from 200 mm/s
- Cut surface roughness Ra<1 µm
- Easy to break after processing
- Smooth edges: minimal or no post-processing needed
- No visible cracks or collateral damage near the cut line
Note: Alternate processing parameters can be developed upon request.
Thin Films / Foil Cutting
Laser cutting by cold ablation process is optimized for each material (plastic film metal foil, and others) that is used. Depending on customer needs focus is on minimal discoloration effects, cutting speed or accuracy.
- Straight & round cut trajectories
- Minimal or no discoloration
- Minimal or no signs of heat -affected deformations
- Excellent cut surface quality, sub-micron precision of shape
- High Speed laser processing
Note: Alternate processing parameters can be developed upon request.
Sapphire Cutting
The laser cutting (scribing) process is optimized for each type of sapphire that is used.
The processing window is wide and can be easily set up according to various parameters.
- Straight & round cut trajectories
- The thickness of sapphire from 100 µm to 760 µm
- Cutting speed 200 mm/s or faster
- Cut surface roughness Ra<1 µm
- Easy to break after processing
- Smooth edges: minimal or no post-processing needed
- No visible cracks or collateral damage near the cut line.
- Different processing parameters might be developed upon request.
Laser Marking
Laser marking on the surface of various materials allows for the creation of logos, images, text, bar codes, security and identification marks or any other plane objects on the surface of many materials with micrometer precision.
Laser Marking Inside Transparent Materials
The main advantage of laser marking inside transparent materials is that information such as: serial numbers, logos, images, bar codes, security and identification 2D / 3D marks can be written directly inside the object by making refractive index irregularities without damaging the surface.
- Colorful structures in glass & sapphire
- Surface not affected
- Very mall or no cracks near markings
- Low influence on the strength of the substrate
- No heat affected zones
- High positioning accuracy (3D marking is available)
Micro Laser Welding
Micro laser-welding enables joining a wide range of transparent materials with transparent and non-transparent materials, like glass-to-glass and glass to metal.
No additional materials are required (unlike bonding processes)- It reduces costs and increases durability. After re-solidification, strong covalent bonds are formed, providing high stability of the joined parts. Dissimilar glasses can be welded with breaking strengths in the range of the volume material.
- High Precision
- Good Mechanical strength
- No extra bonding material needed
- Hermetic sealing
- Minimum heat -affected zones
Laser Surface Structuring
Workshop of Photonics has a long-term experience in femtosecond laser surface micro-structuring.
Free from thermal effects pulses enable the creation of precise structures for desired applications.
A large Variety of nano and micro-scale structures can be controllably produced on diverse metallic and transparent materials that use direct femtosecond laser processing techniques.
Selective Laser Ablation
Selective laser ablation is one of the most common industrial lasers application today. It ensures high processing speed and high quality of a processed area.
Small portions of metal layers can be precisely removed without any damage to the substrate using femtosecond laser pulses. The depth and geometry of ablation can vary so it is suitable for a variety of applications.
- High-speed laser processing
- No signs of burning
- No heat effected Zones
- High positioning accuracy
- High quality
- Micron resolution
Hard Materials Ablation
Ablating hard materials such as polycrystalline diamond (PCD) and sapphire is a challenging task even for lasers.
This task can be managed by using a femtosecond laser that overcomes not only the hardness of materials but also very high thermal conductivity which allows us to avoid burned regions that can appear if other methods are used.
- Production of Lithography Masks
- Beam Shaping Elements
- Optical Apertures
- Diffraction Gratings
Multiphoton Polymerization MPP | 2PP
Workshop of Photonics for over 15 years is working on novel systems development for various research groups and companies. Technologies entering the miniaturization era have encouraged the pursuit of 3D Additive Manufacturing Development.
- Writing Resolution: <150 nm (typ.200 nm)
- Ability to change writing resolution during writing process
- Variety of polymers available (commercially available & only recently developed materials)
- Stitching error-free laser writing
- Fabrication of complex 3D objects and arbitrary microstructures
- Repeatability and stable workflow
- Possibility to in-situ integrate new structures into existing ones
3D Additive Manufacturing (MPP)
Point-by-point laser writing in photoresists is a unique technology for 3D structuring of nano-micro- meso- and macro-scale printing.
It is also referred to as:
- Multiphoton Polymerization (MPP)
- Two-Photon Polymerization (TPP, 2PP)
- 3D Laser Lithography (3DLL)
- Or simply Direct Laser Writing
Send your product drawings or concepts and our technical staff will recommend the best manufacturing process for your application.
We offer free sample processing in our Applications Lab to confirm process feasibility and final product quality. Upload your part drawing files or sketches on our Contact Us form below.
Please contact us – we are ready to assist!